360° special optical lens series Beautiful images with a single camera vs multi-camera system
© Optart Webmaster
This article was featured in the September/October issue of Eizo Joho Industrial, published by Sangyo Kaihatsu Kiko Co., Ltd. This article is published with permission from the copyright holder, Sangyo Kaihatsu Kiko Co., Ltd.
Development Background: Unique Technology and Advantages
One of the most popular requirements from the machine vision market is to see more of a specimen with a minimum amount of imaging equipment, which is especially common in the food and beverage, machinery, and medical industries. In these cases, machine vision systems are required to simultaneously analyze many different areas of a specimen, or are used to identify irregularly occurring defects. The first traditional approach to solving these problems was to use multiple cameras, but this approach has three drawbacks:
- - The device takes up space and has a complex structure: The appropriate working distance for each lens needs to be considered, and it is complicated with cables, power supplies, etc.
- - A large number of cameras requires a variety of calibrations.
- - Installation and maintenance costs are high.
The second traditional approach is to use line-scan technology, but this also has the following disadvantages:
- ・When the subject (workpiece) is a three-dimensional object, handling is complicated: If inspection of the workpiece in all directions is required, the workpiece must be rotated 360° within the lens's field of view, or if this is not possible, the lens including the camera must be rotated around the workpiece. Either way, a transport device is required to rotate the workpiece or rotate the camera and lens, and the speed is naturally not fast, so it is not suitable for online inspection using line scanning.
With this in mind, Opto Engineering decided to design a specialized group of lenses for these applications: the 360° Optics series.
Technical Examples
Despite the different access techniques, all lenses in the Opto Engineering 360° series deliver the same result: they provide a single image with information on the inside or outside of the specimen. The image is provided as a whole in the PC, PCCD, PCHI and PCBP series, or segmented by angle in the TCCAGE, PCPW and PCMP series. They cover a range of diameters, from large ones over 50 mm to small ones under 10 mm, with different aspect ratios between diameter and height (Figures 1-7).
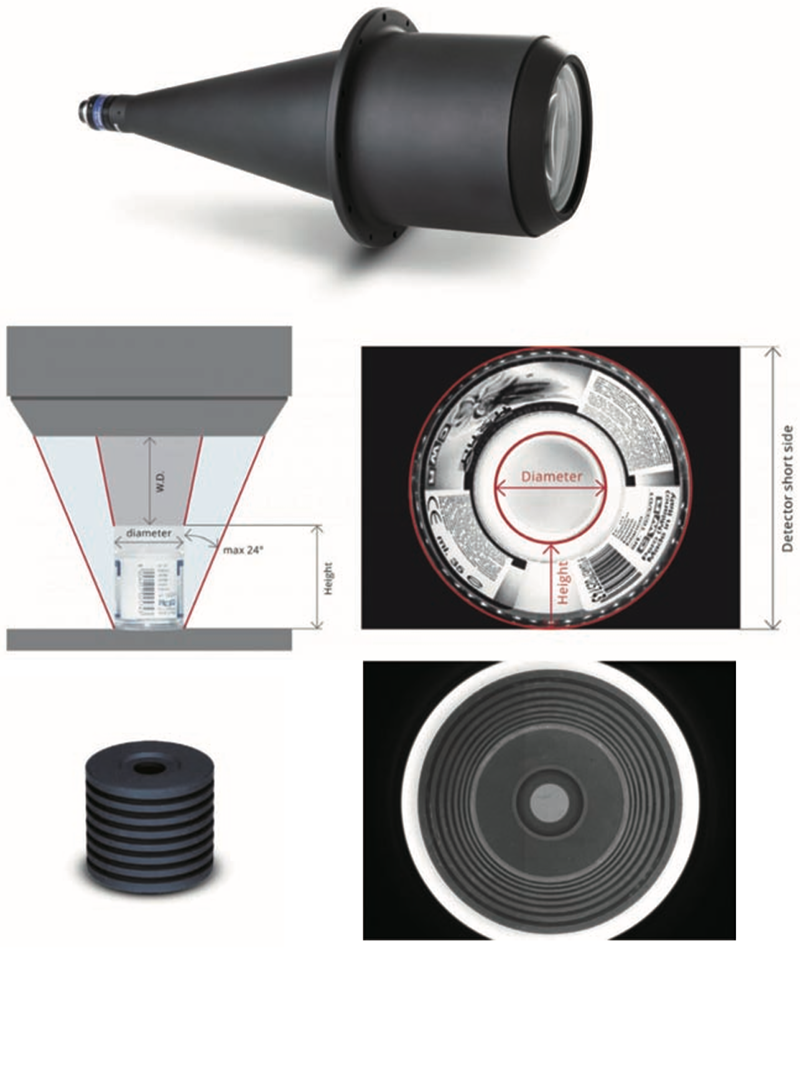
A lens that can capture images of the outer periphery and top of a workpiece up to φ60 x 20 mmD from 360° directions with a single camera while being away from the workpiece.
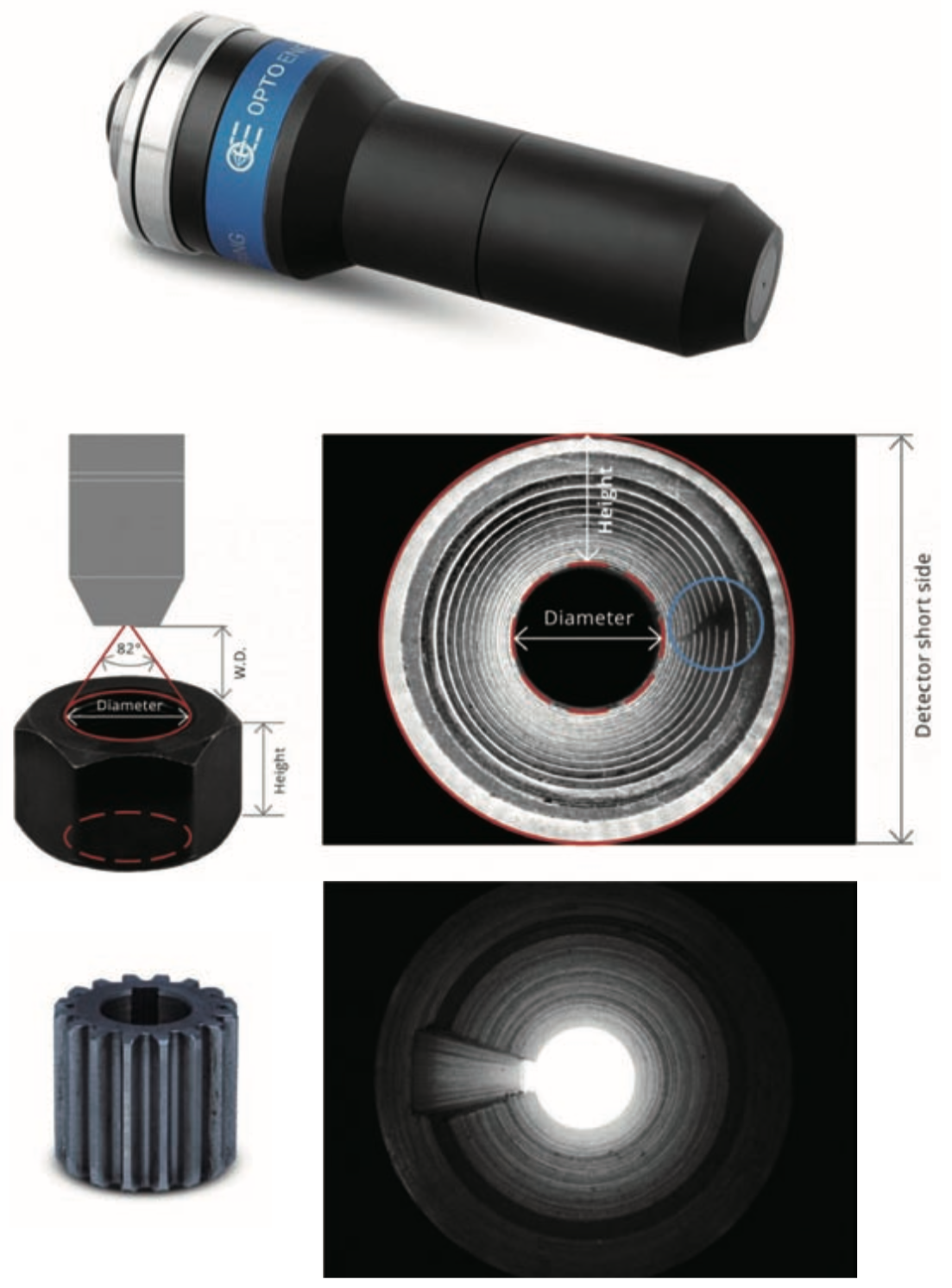
A lens that can capture images of the inner surfaces and bottom surface of a workpiece up to φ120 x 90 mmD with a single camera while being away from the workpiece.
Application Examples
An interesting application example is the inspection of the inner surface of engine rings. Among many automotive parts, engine rings are very important components, even though they may look simple. Even a small surface defect can prevent the component from working efficiently and shorten the lifetime of the whole system, or in the worst case, lead to early failure. Such critical component defects should be detected at an early stage, especially in the manufacturing process aiming at improving quality and reducing costs. Machine vision should play a fundamental role in such an area.
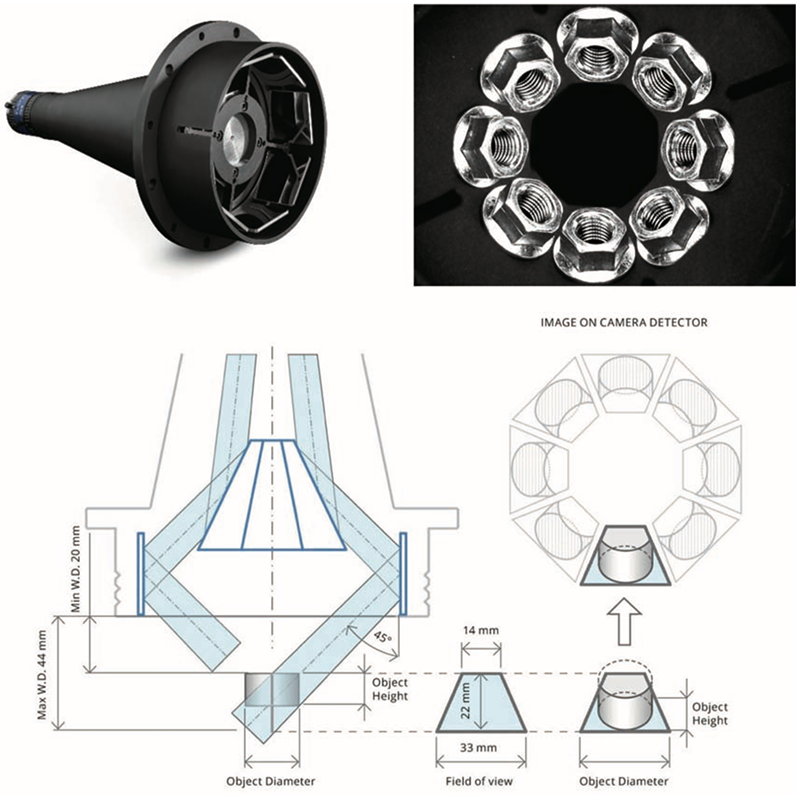
The built-in eight-sided mirror projects an eight-sided panoramic image of one workpiece.
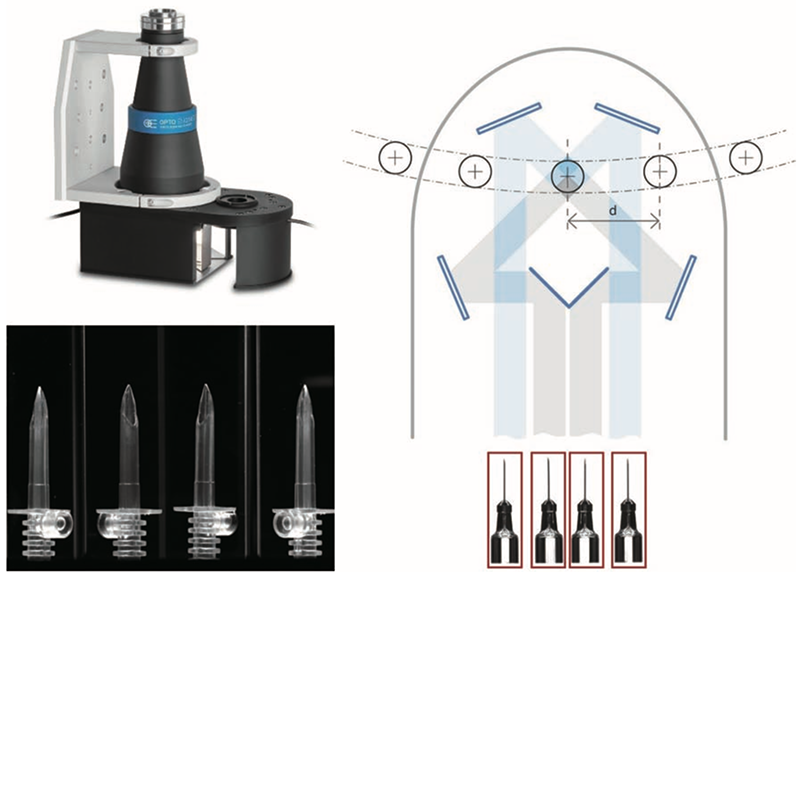
The built-in four-sided mirror displays a 360° image of a single workpiece as a panoramic image with four sides at 90° each.
A customer requested us to design an inspection system that can detect surface defects on engine rings of different sizes, especially defects found on the inner surface. For example, the diameter of the rings ranges from about 25mm to 76mm, and the height ranges from 4mm to 20mm. The customer wants to inspect the outer or inner side of the rings for defects such as cracks of about 200μm with a single camera. For the inner surface inspection, the customer chose Opto Engineering's PCHI023 Hole Inspection 2/3 inch camera to get a perfect focus view of the inner side of 360°. With a large viewing angle of more than 82 degrees and an innovative optical design, PCHI023 is practically compatible with a wide range of holes from 10mm to 120mm, and is suitable for cylinder, cone, hole, bottle, and screw thread observation.
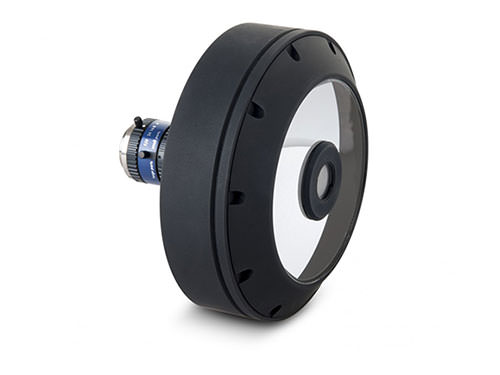
While separated from the workpiece, a single camera captures the outer surface and top image of the workpiece up to φ25×17mmD from 360° directions. Lightweight and compact design compared to the Pellesen Tri-Lens PC series.
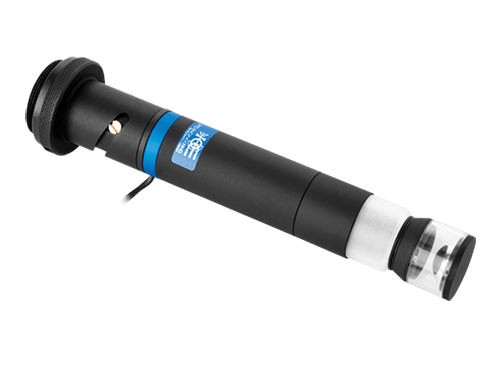
Insert into a pipe etc. to capture images of the inside surface of a workpiece with a maximum inner diameter of φ100 x 53mmD. With a built-in white LED light source, it is ideal for inspecting the inside surfaces of processed parts and containers made of metal or resin.
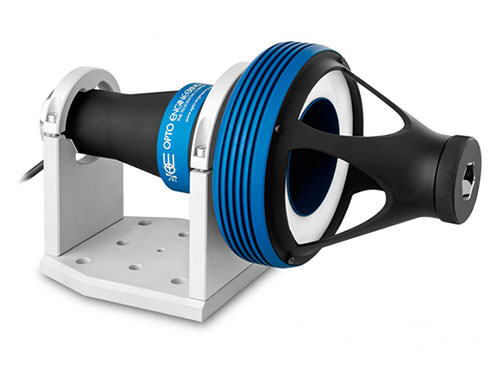
The built-in mirror projects a front image and a 6-sided panoramic image of the workpiece. Ideal for inspecting scratches on the inside and outside of metal or resin processed parts and containers.
About the Technology Roadmap
Today's industry is moving towards simplicity, speed and high performance. Opto Engineering's 360° product line is on the same roadmap, and we strongly believe that simplicity leads to better workability. Therefore, we will continue to pursue the development of these specialized lenses to better meet the needs of our customers and the market. We will continue to challenge ourselves to meet the needs of smaller hole diameters, high resolution lenses, and diversity of mechanical dimensions.
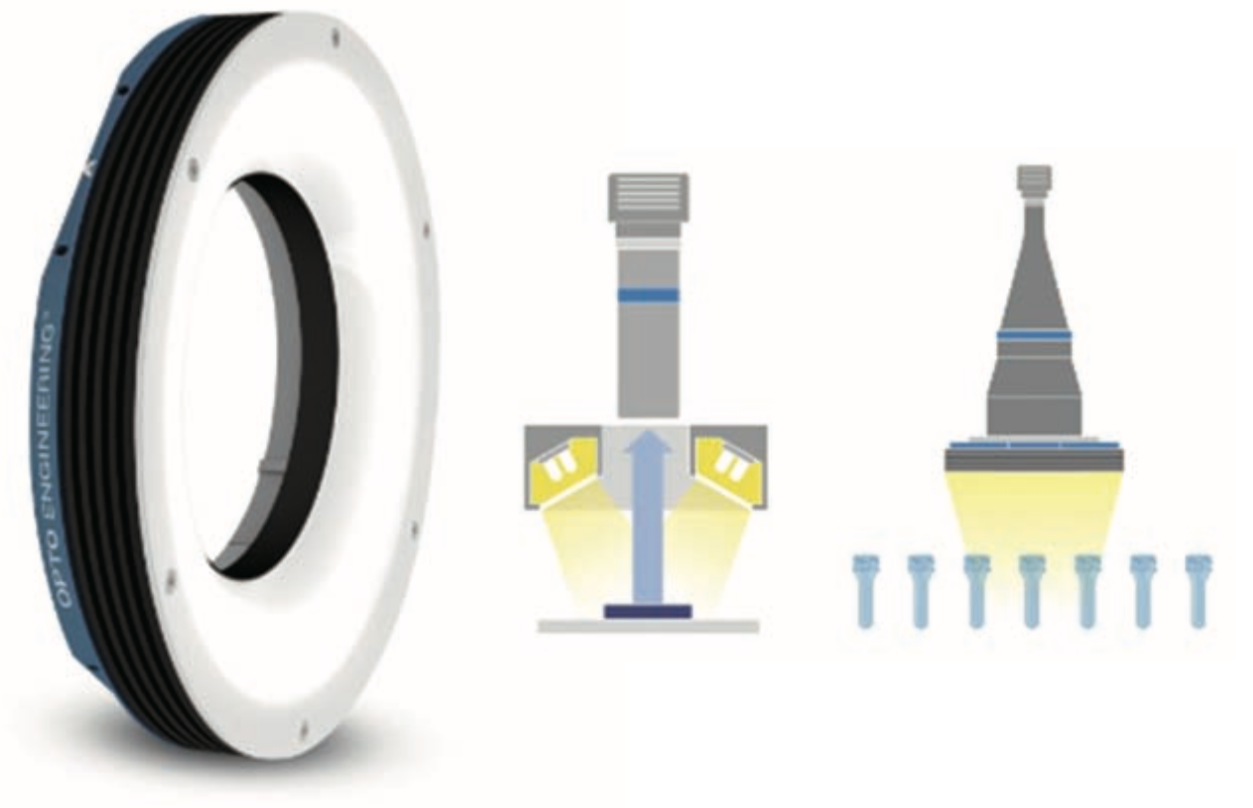
Several developments are already underway. From the creation of the more powerful ring lighting device LTRNOBHP series (Fig. 8), we have begun to offer a variety of never-before-seen products, such as the 360LIB Suit, and we will continue to provide the world's best solutions for 360° optical systems to suit your applications.